Case Studies
Development Of Customized Software For Simulation Of Gas Turbine Compressor
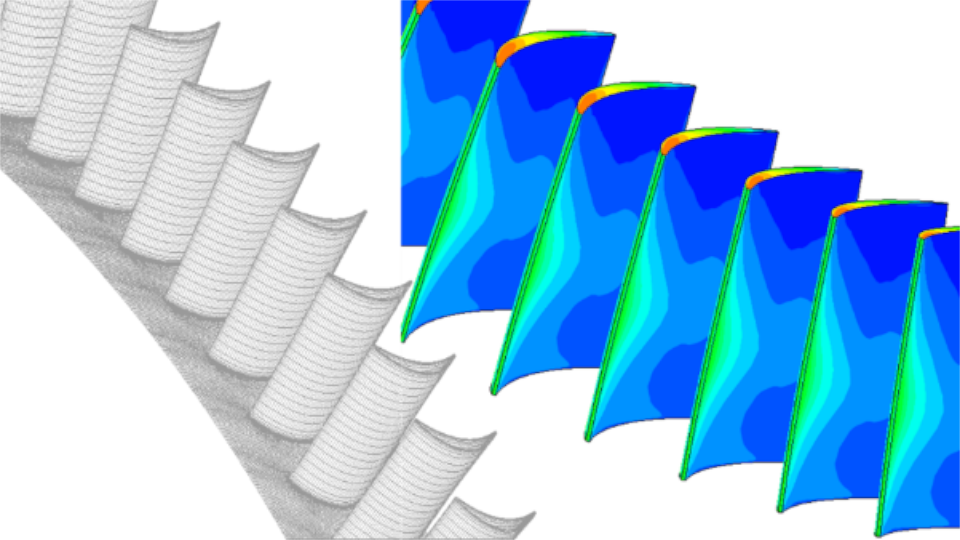
Our customer is responsible for design and development of gas turbine engines with active research on multi-stage compressors. The designs suffer from stall and surge problems and customer wanted to develop an automatic and reliable CFD tool for predicting the flow characteristics around the compressor blades. As the simulation of any rotating machinery takes a lot of time, to speed up design, customer wanted the code to be massively parallelized on a large HPC system.
Density based compressible solver was developed for the simulation with the rotating sections modeled as mixing planes. Spalart Allmaras turbulence model was used to predict viscous effects. First phase of the project was only for validation where NASA CD Nozzle, Sajben duct, Rotor 37 and Rotor 35 were simulated. In the second phase, the customer gave its own geometry for simulation.
Validation for NASA Rotor 35 were within 4-5percentage of the experimental values. The code gave accurate results for other validation cases too. Multi-stage rotor of 120 blades designed by customer was then meshed with all the passages modeled without the need of periodic boundary condition. Structured multi-block mesh was made of 1440 blocks and 12 million mesh points. Code was made parallel to run on large HPC system and CDAC PARAM Yuva II HPC was utilized for studying the scale up. The customer was delivered with a customized software for simulation of compressors on their HPC system.
Previous
Parallelization Of Stealth Software For Full Aircraft Rcs Prediction
Preceding
Assessment Of Nose Shape And Taper On Aerodynamic Stability Of Missiles
...