New Product Development
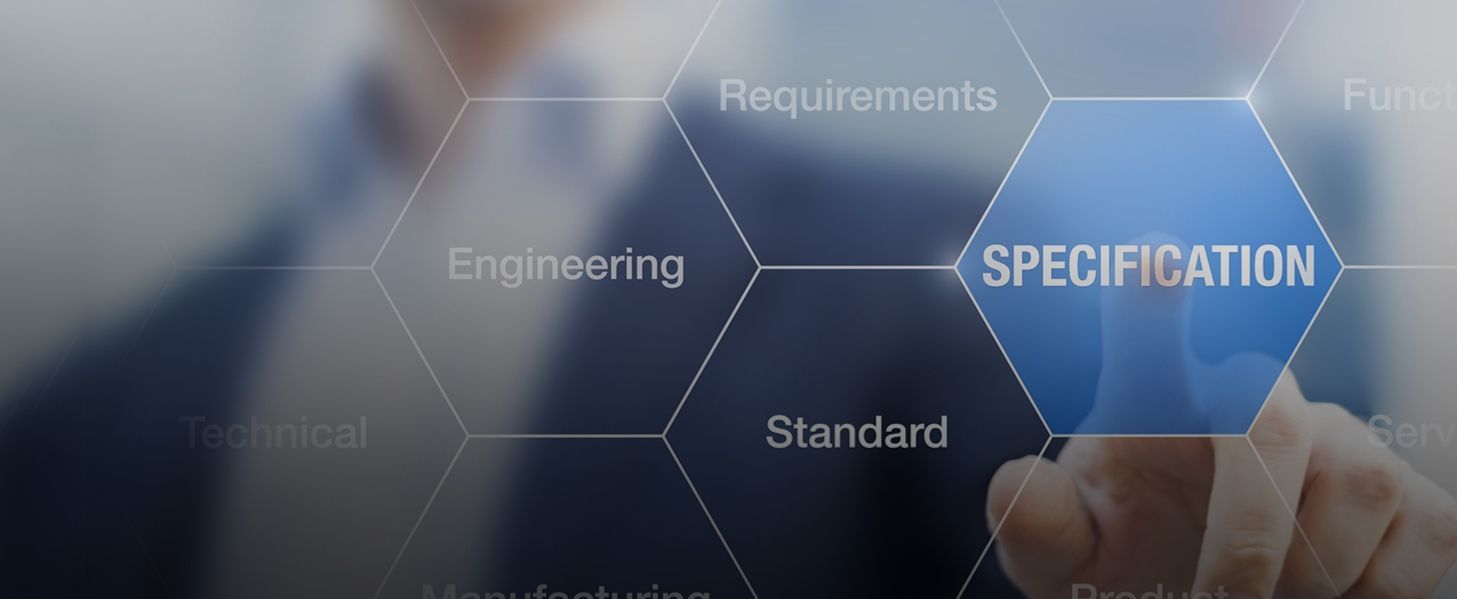
New Product Development
We partner to deliver best in class designs that are backed by numerical models and analysis. Given the specs, we undertake conceptual design, detailed design, performance estimation & finally release manufacturing drawings for the customer. Our association follows into testing and trial phases, culminating in products that meet the desired requirements. Our experience includes material handling equipment, turbo-machines, test rigs & certain classes of defence equipment.
Areas of Work
- Products for mechanical and electro-mechanical systems
- Metal and composite products on civil or military specs
- Testing rigs with sensor integration and SCADA
- Electronics products for controls
- Fluid machinery products for civil and aerospace applications like pumps
Development Process
- Design from first principles and Design by Analysis
- Design for manufacturing, GDT and cost optimization
- Manufacturing partnerships with large companies and innovative SMEs
- Testing and validation before delivery; design of testing equipment
- Transfer of IP as per contract
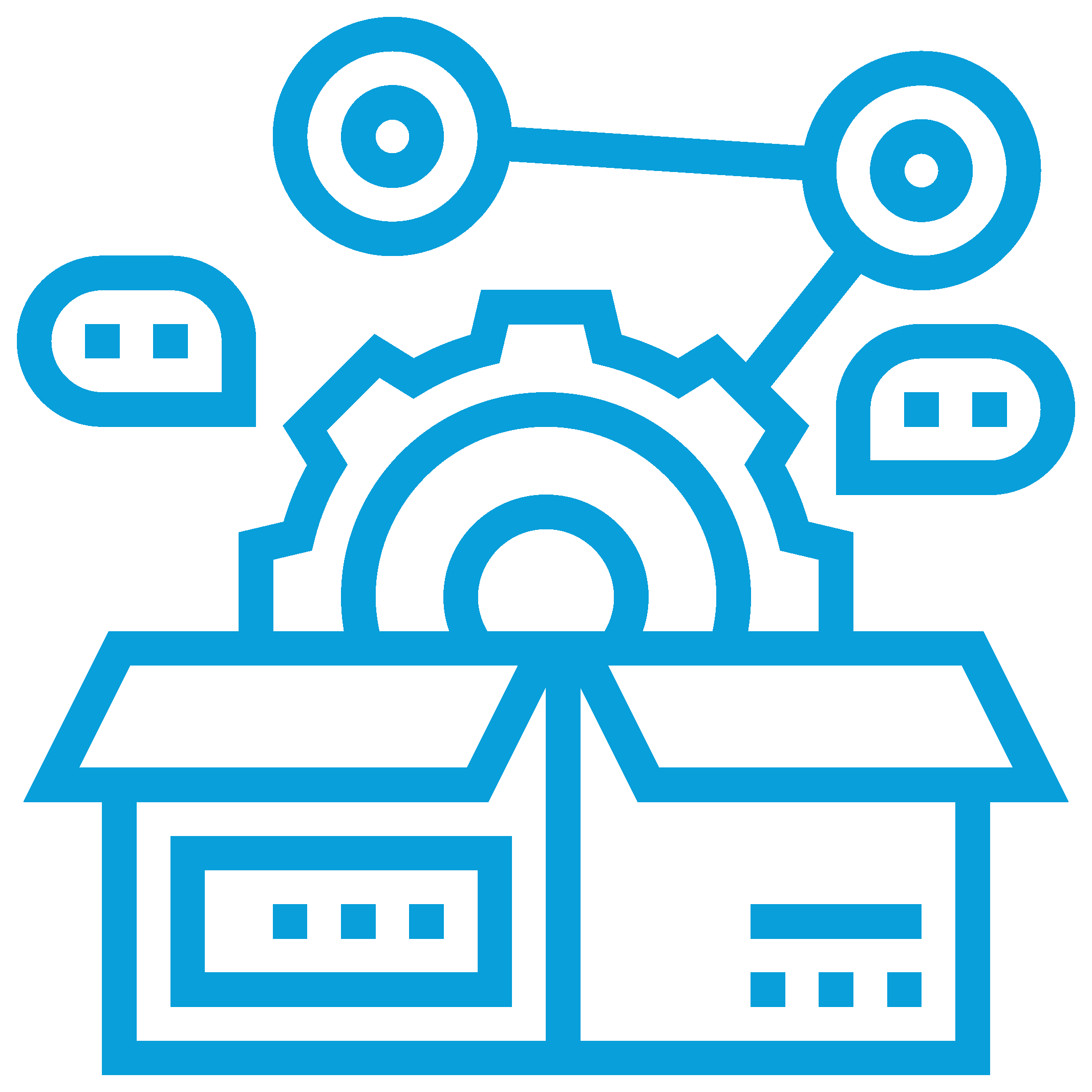
Design Conceptualization
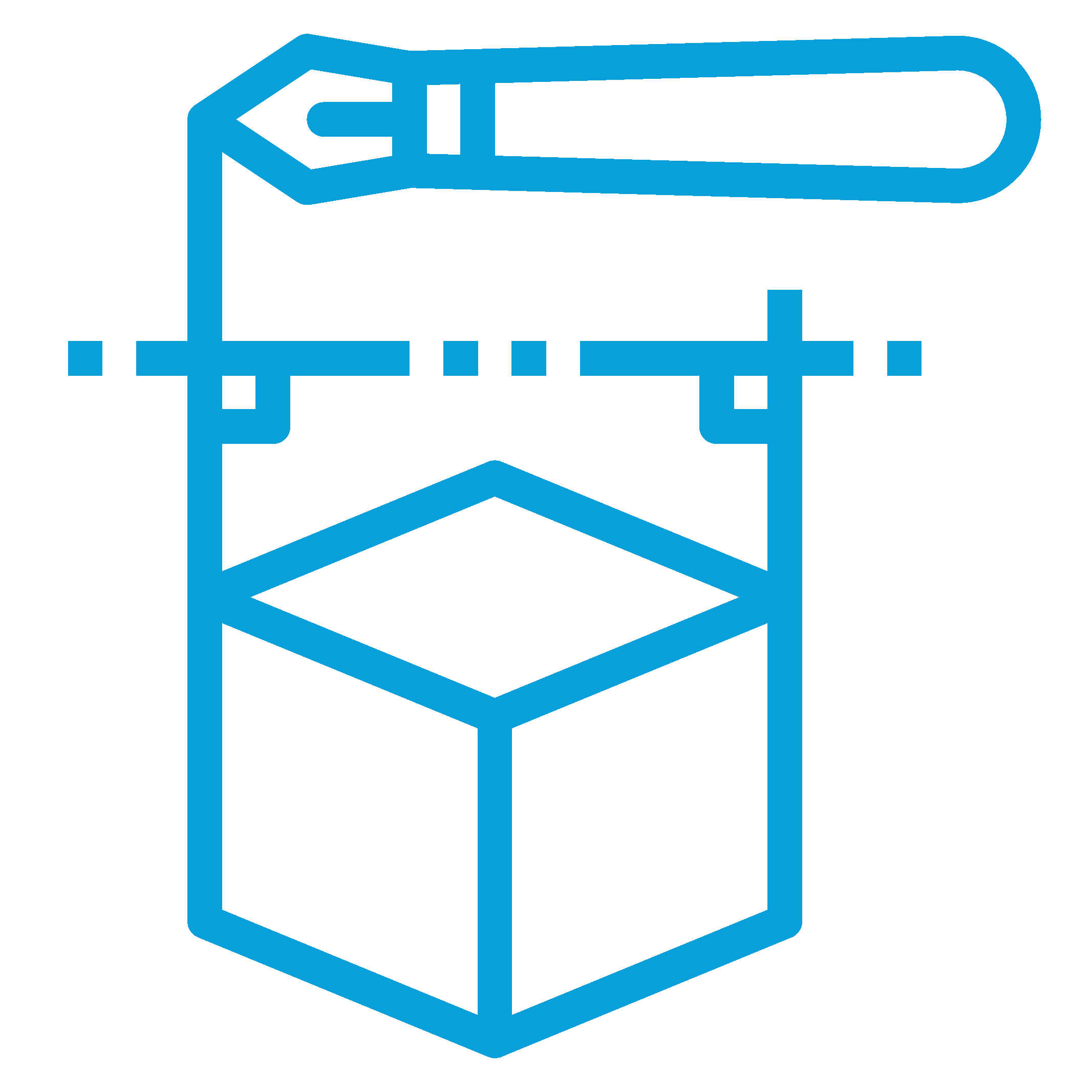
Detailed Designing
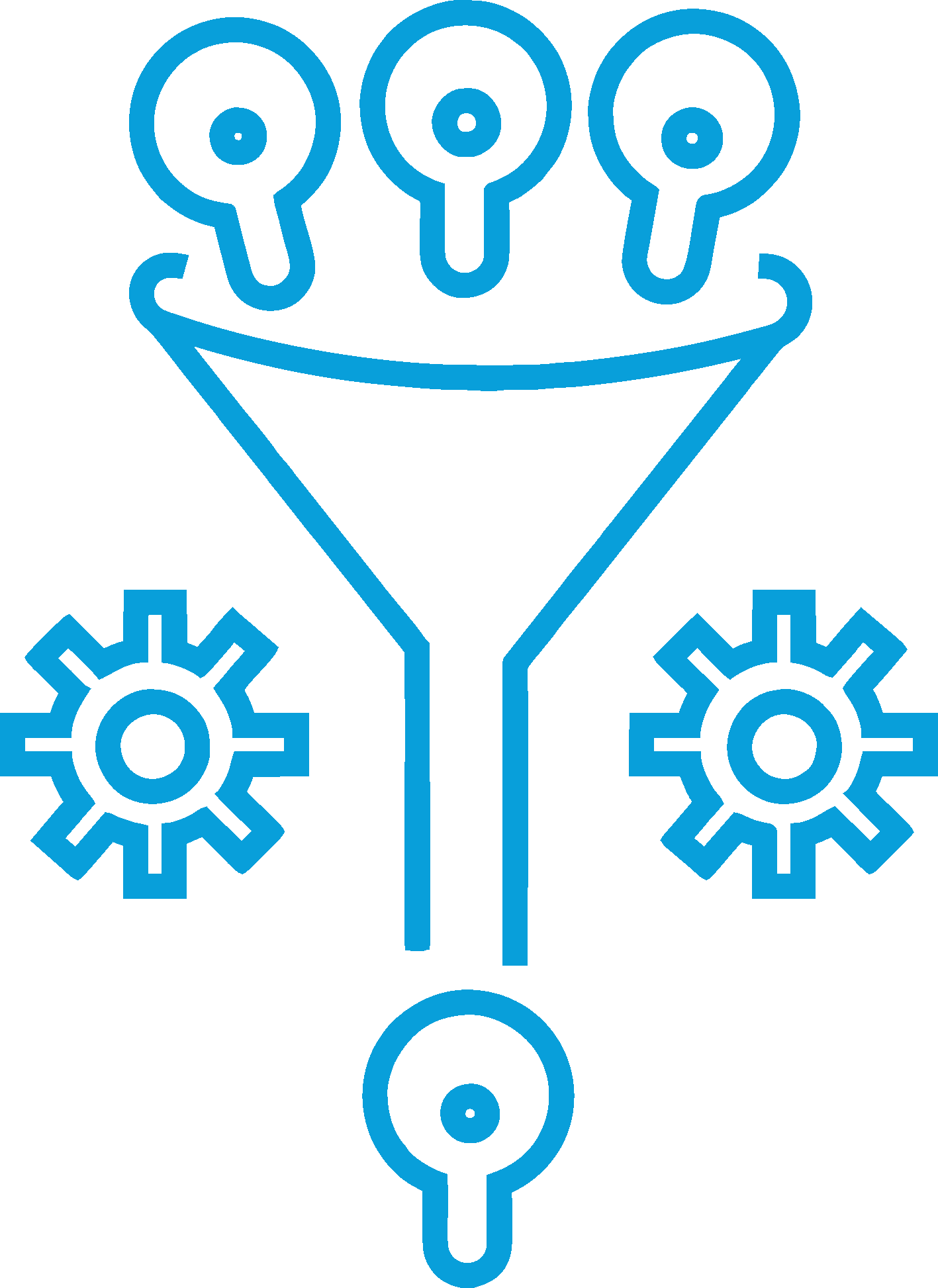
Design Refinements
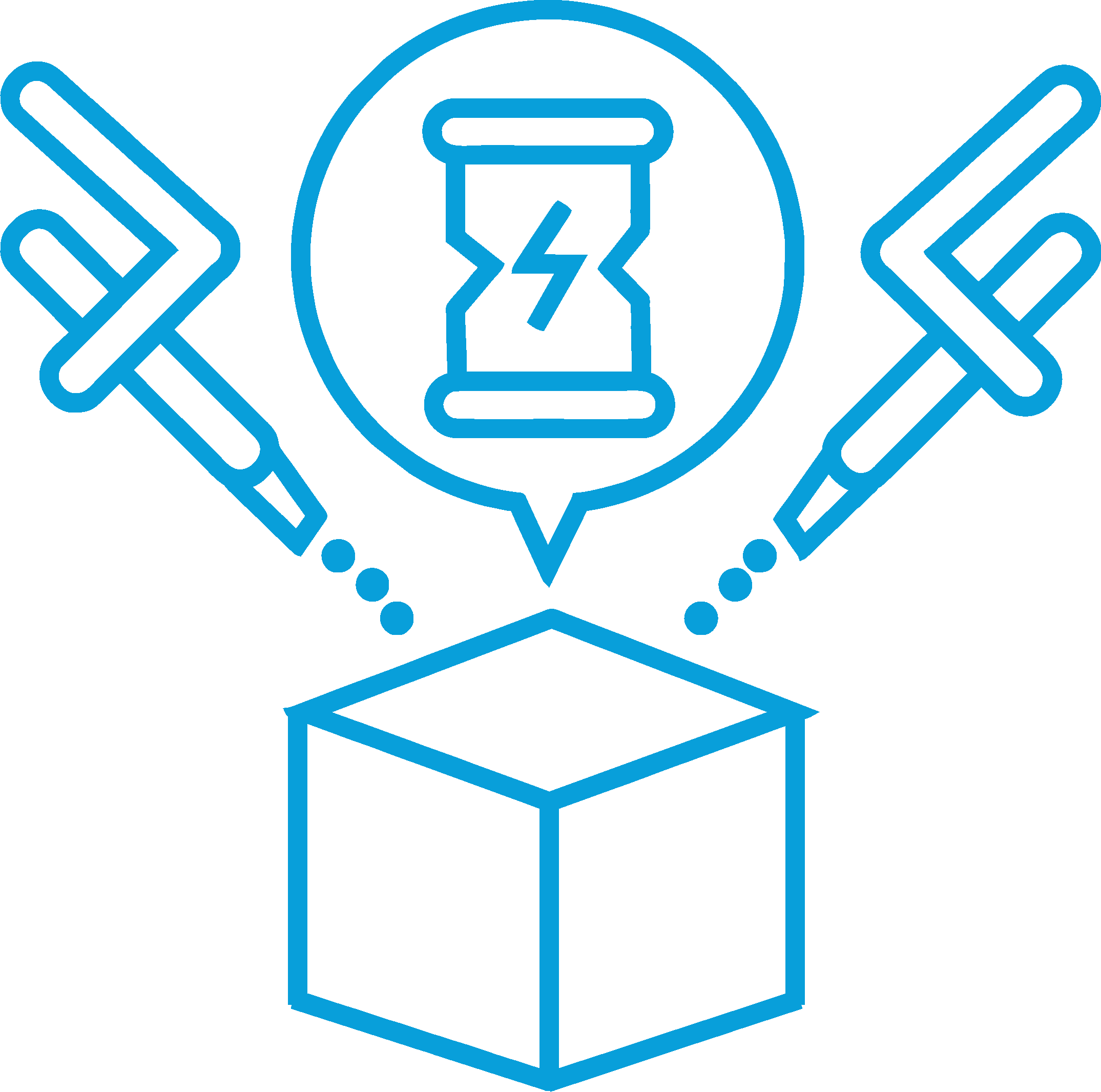
Rapid Prototyping
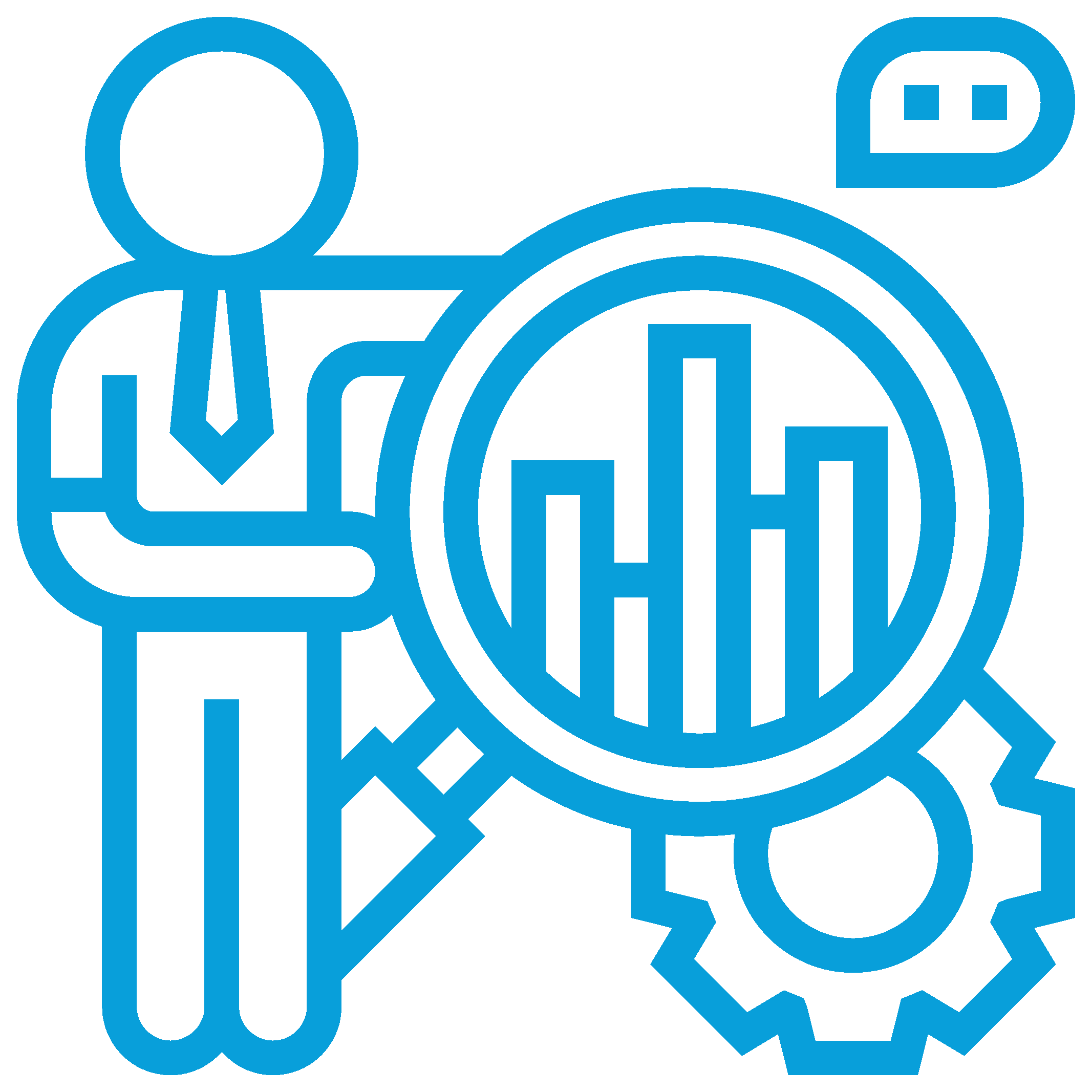
Testing
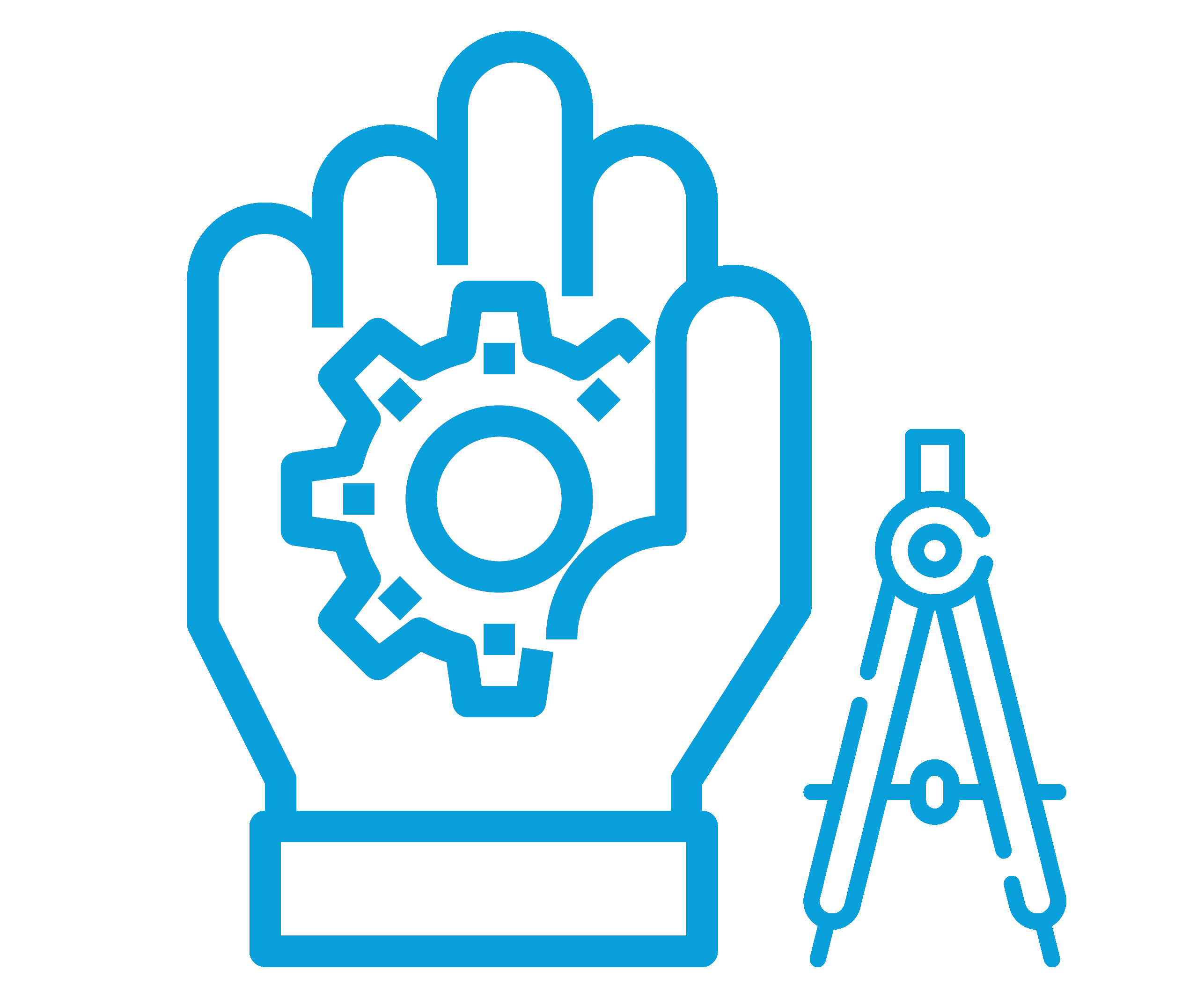
Fabrication Drawings
Any new product development initiates with the design thinking process. Design thinking is a user-centric approach, which employs an iterative process to understand product specifications and to document the means to attain them. The process ensures that all stakeholders are consciously aware of complete user and product requirements early in the design phase. There are no corrective actions after the product has been launched for user exploitation. Corrective design modifications can be extremely costly especially, after processes, infrastructure and tools have been developed for bulk manufacturing.
The product requirements can be categorized as functional, performance, operational, safety, reliability, maintainability, installation, interface, certification and documentation. A quality assurance plan (QAP) document is followed that tracks raw materials, manufacturing processes & dimensional adherence. Each new product has to undergo qualification and acceptance trials. Qualification trials are done only once on the prototypes to verify and validate the design of the product. The qualification trials are harsh and extensive. On the other hand, acceptance trials are done during bulk production to validate the performance of the manufactured product.
Case Studies
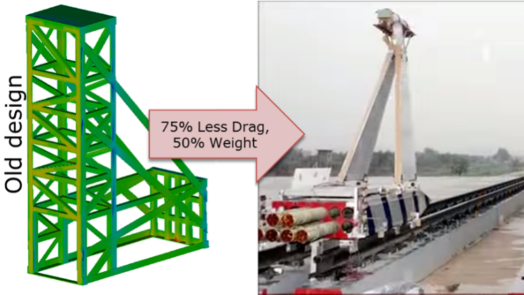
Design and Development of Supersonic Rocket Sled
The lab uses a rocket launched rail track facility to do high speed measurements on various payloads....
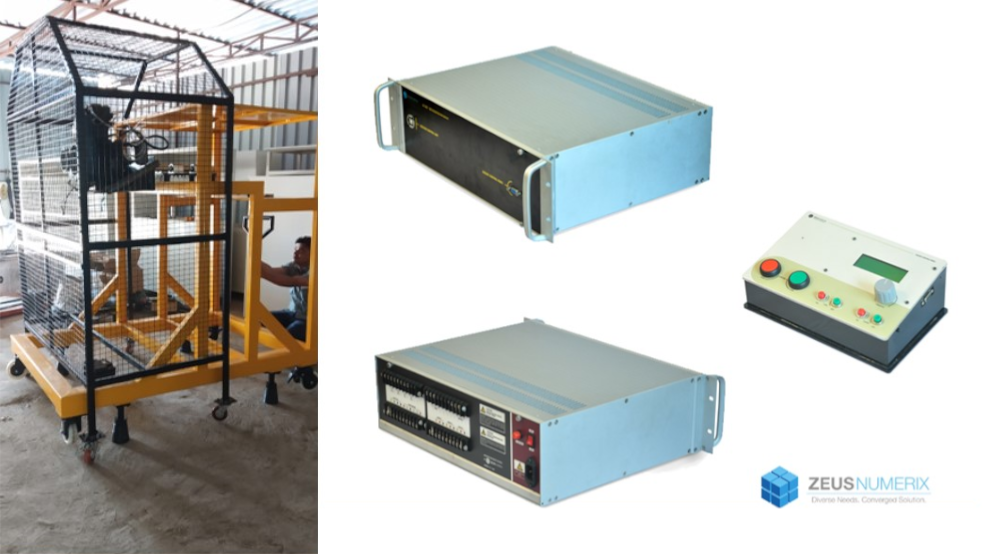
Design, Development & Supply of Thrust Cradle for Testing IC Engine of Airship
The thrust cradle should be able to do ground testing, performance evaluation & measurements...
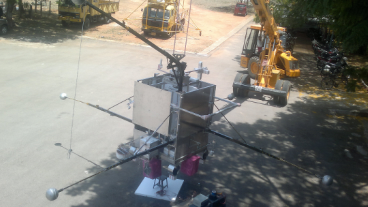
Design and Fabrication of Deployable Boom
To conduct high altitude balloon experiment for measurements of electric and magnetic field...