CAE Simulation Services
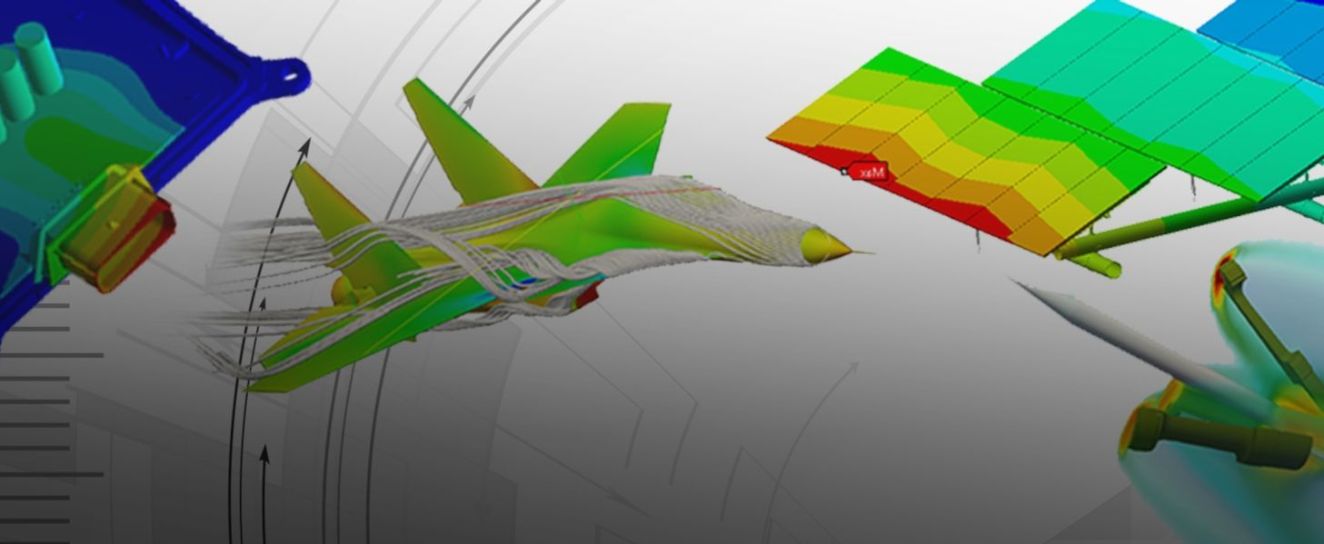
CAE Simulation Services
We offer on-demand CAE services for simulation requirements in multiple disciplines and across sectors. The diverse experience of 15+ years allows us to select the most suitable method from commercial, open-source & proprietary CAE software. We ensure that our customers are made fully aware of our modeling approach and solver assumptions. Our team engages to not only explain the simulation results but also suggest design changes so those simulation objectives are fully met.
Our Uniqueness
- Ownership of intellectual property of tools in CFD, FEA, CEM
- Experience of 450+ projects and 15+ years of existence
- Domain expertise in various industrial sectors
- Unconventional or niche simulation expertise
- Stealth characterization and Radar cross-section reduction
- Experience on commercial and open-source platforms
Technologies we work
- Computational geometry and modeling
- Mesh generation and post-processing
- Computational fluid dynamics (CFD), Finite Element Analysis (FEA)
- Computational Electromagnetics (CEM)
- Dynamics, Controls, Guidance, Navigation and electronics
- High-performance computing, parallel processing
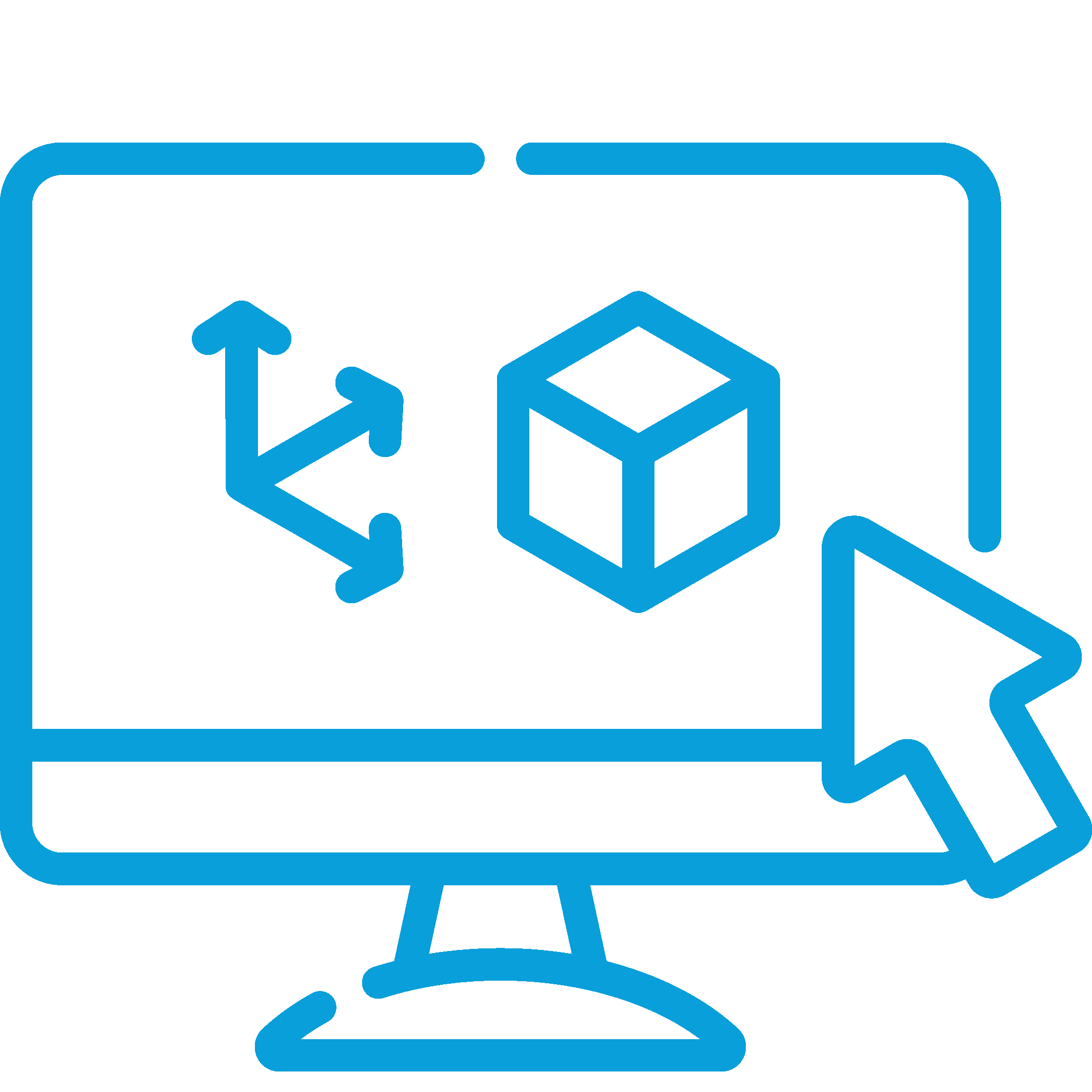
3D Modeling
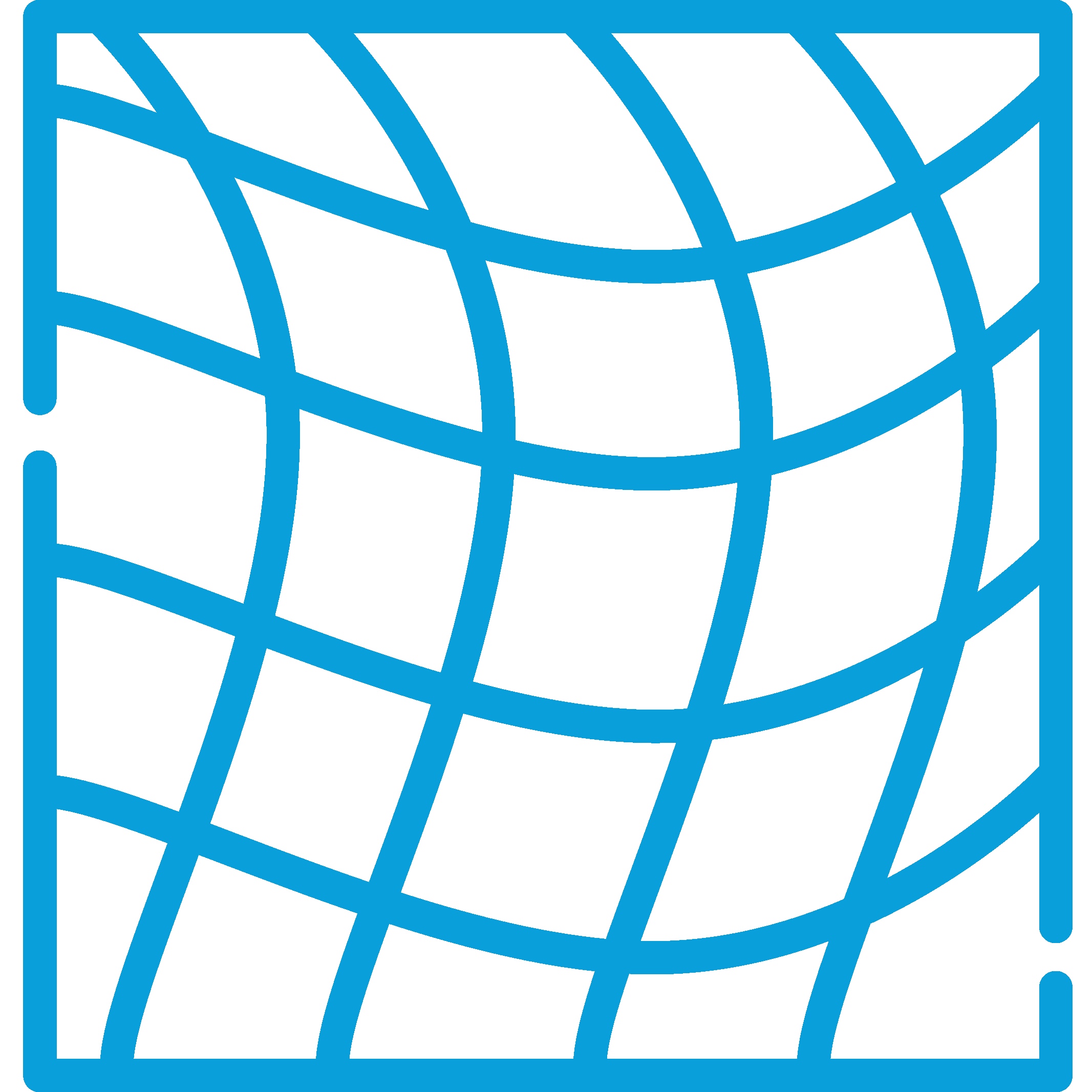
Mesh Generation
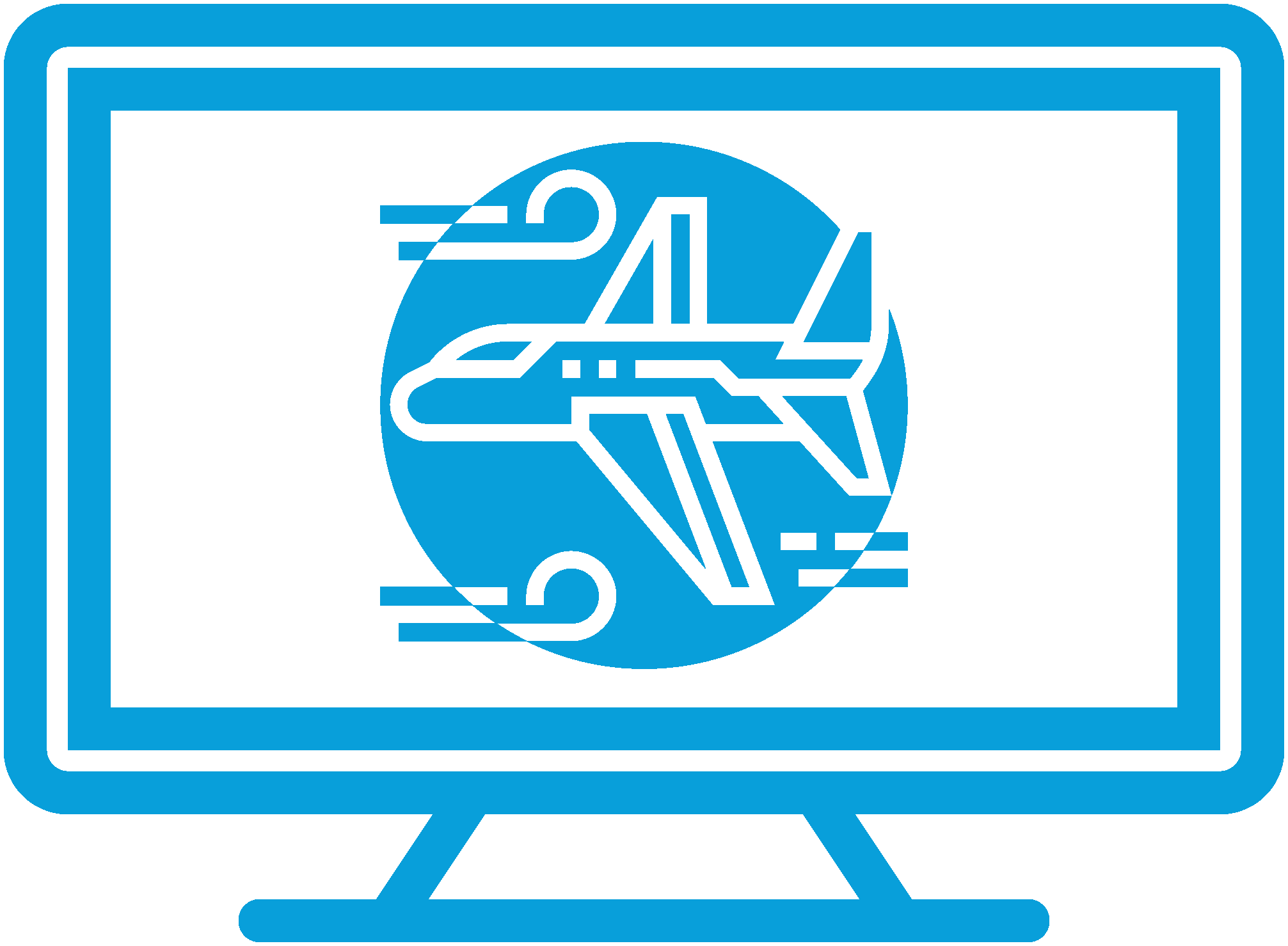
CFD Analysis
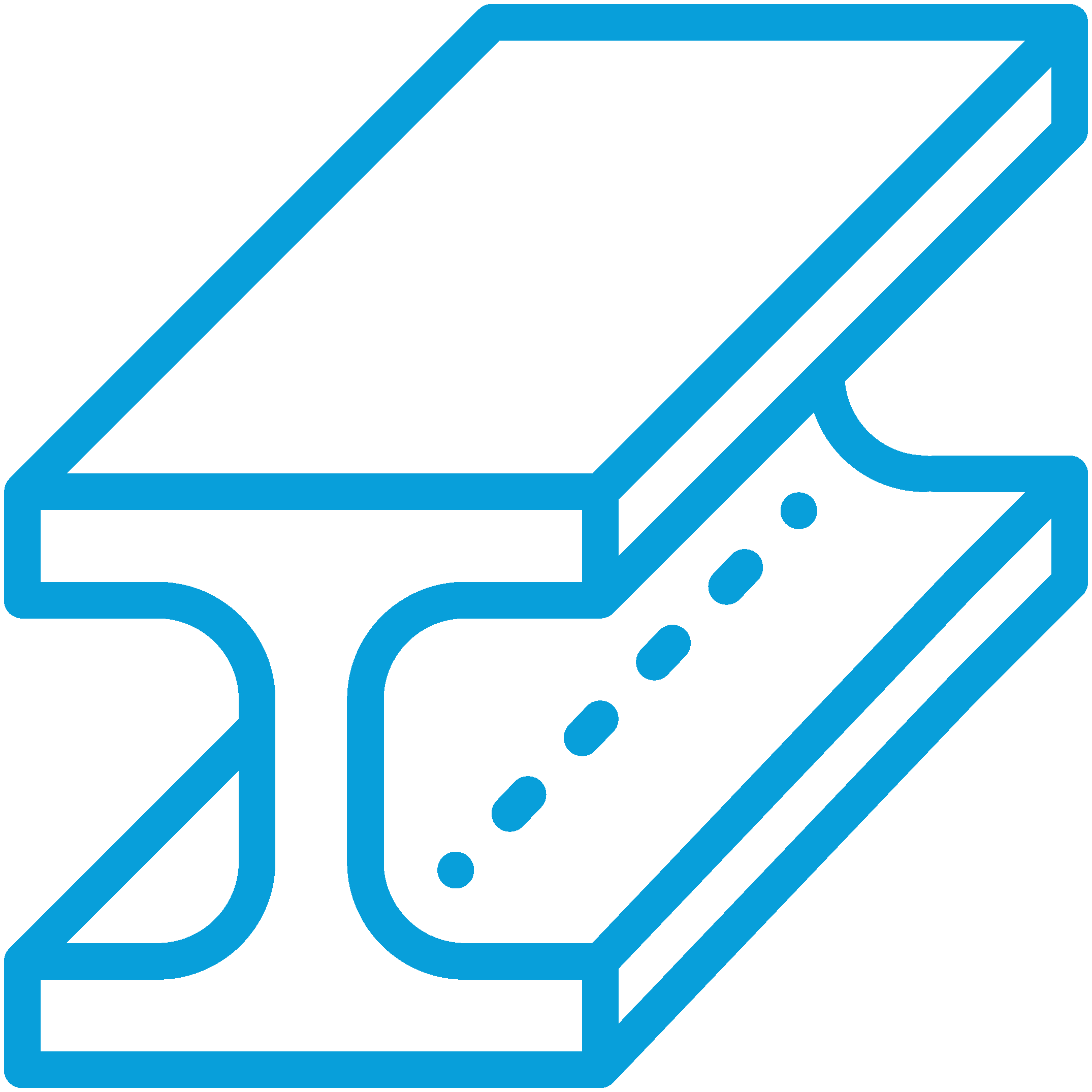
FE Analysis
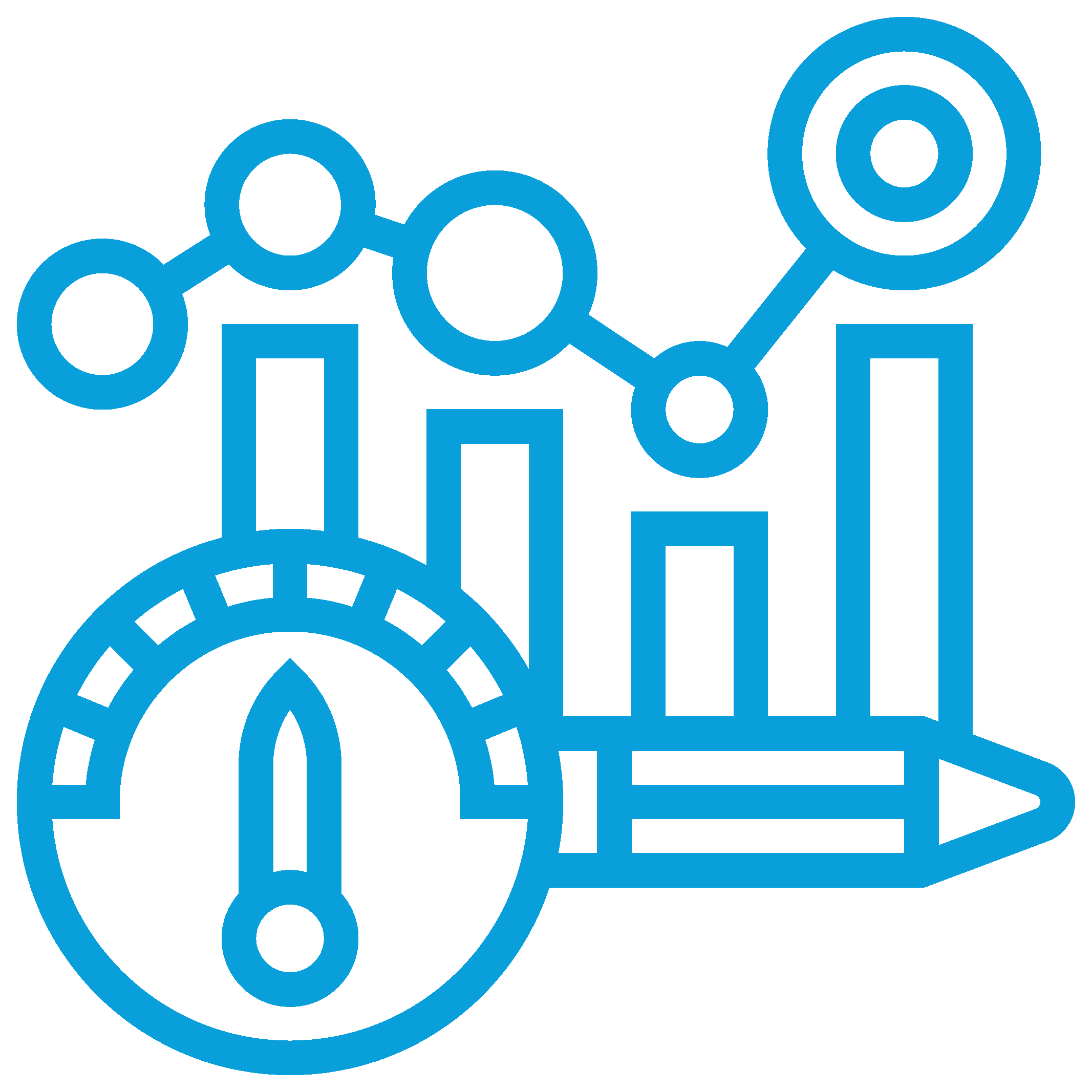
Design and Performance Optimization
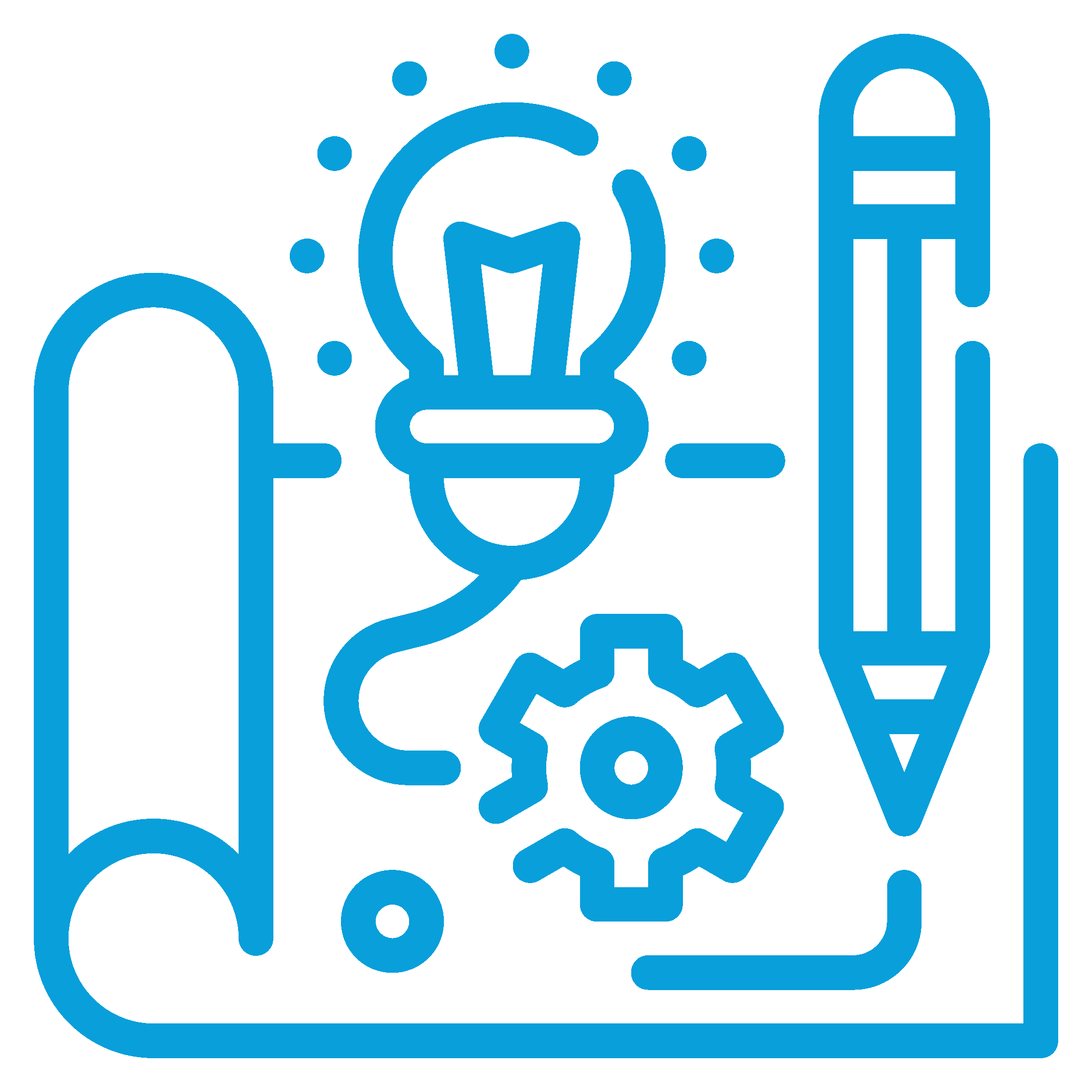
Multi-Disciplinary Physics
Computer-Aided Engineering (CAE) is the process of performing engineering analysis tasks. These engineering analysis tasks are done over the product's 3D CAD computer models. Common CAE simulations include CFD, FEA, and MBD, simulations. It also includes optimization through analysis. Any conventional CAE simulation involves six processes. They are modelling, meshing, case setup, simulation runs, post-processing, and analysis of results. The first step of any CAE simulation is a model idealization. This process involves the simplification of the geometrical details. Geometric details which are not relevant is removed. Idealization leads to less number of mesh elements enabling smaller computational time.
Meshing is the process of discretization into a network of cells and points. Governing equations that are in the form of partial differential equations (PDEs) are solved over this mesh. Each cell of the mesh represents an individual solution of the equation, where governing equation must be satisfied CAE solvers combine the solution of these cells to create the actual solution for the entire mesh. Mesh independence study is done to ensure that results obtained are not dependent on numerical factors such as mesh density. Modern CAE simulations make use of HPC computing power to perform the simulations faster. CAE’s post-processing module allows visualization of CAE simulation results. The module provides surface contour plots, streamlines, hot spots and iso-surfaces for visualization of the results.
Case Studies
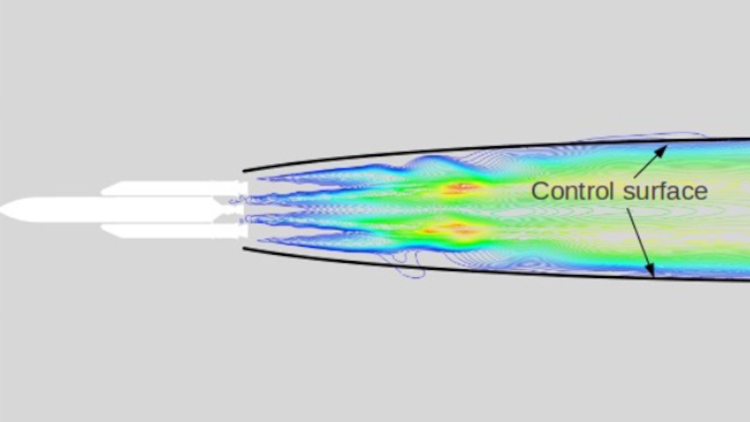
Estimation of Unsteady Pressure Field for Space Vehicle
Estimating unsteady pressure field exerted on the external surface of launch vehicle during its ascent for...
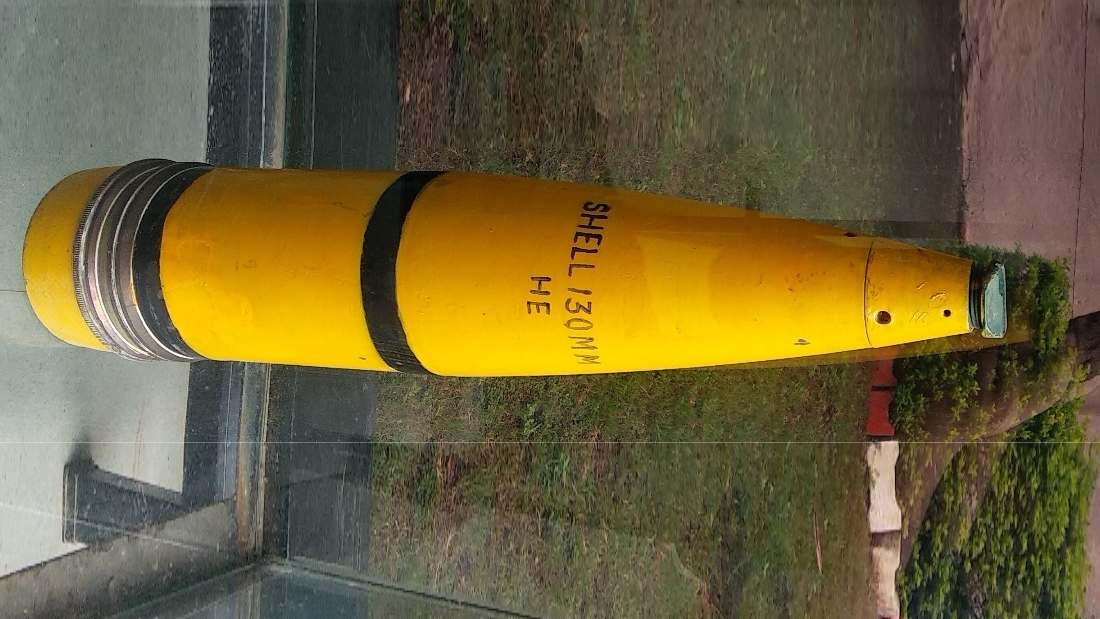
Structural Analysis of Artillery Shell During In-Bore Travel
During in-bore travel, the shell is subjected to large amounts of loads typically due to axial acceleration and...
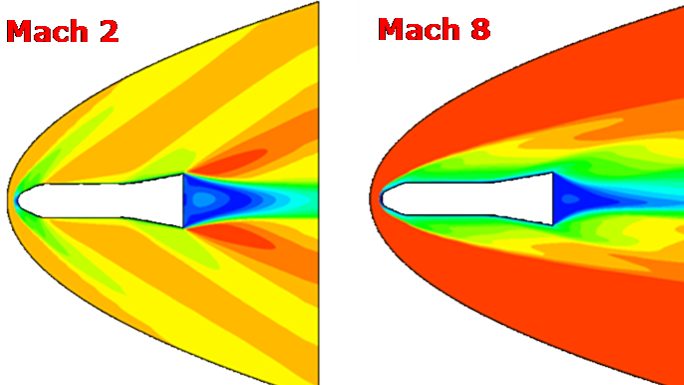
Assessment of Nose Shape and Taper on Aerodynamic Stability of Missiles
Guided Missile missiles will travel at hypersonic speeds with interception range up to 5000 Km...