Heavy Equipment
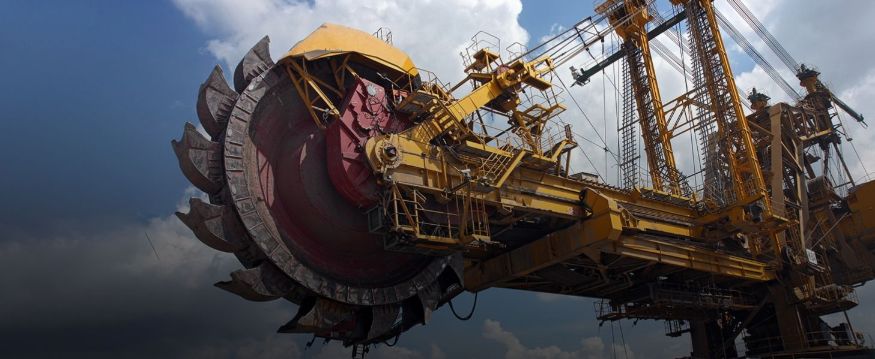
Heavy Equipment
Heavy industrial products are under the constant pressure of cost reduction. At Zeus Numerix, our focus is getting the maximum return for your material, component & manufacturing costs. While doing so, we verify and validate to ensure that the performance and high-reliability standards of your products are not compromised. We specialize in material handling products, automotive components and equipment used in renewable and conventional power plants.
What we offer
- Design optimization through value engineering
- Linear and non-linear finite element analysis
- Shock and vibration analysis
- Heat transfer studies
- Engineering design calculations
- Software development for multidisciplinary engineering solutions
Whom do we serve
- Solar, wind, hydel industries
- Nuclear power industries
- Automotive sector
- Heavy-duty equipment OEMs
- Metal processing and metalworking industries

Cranes
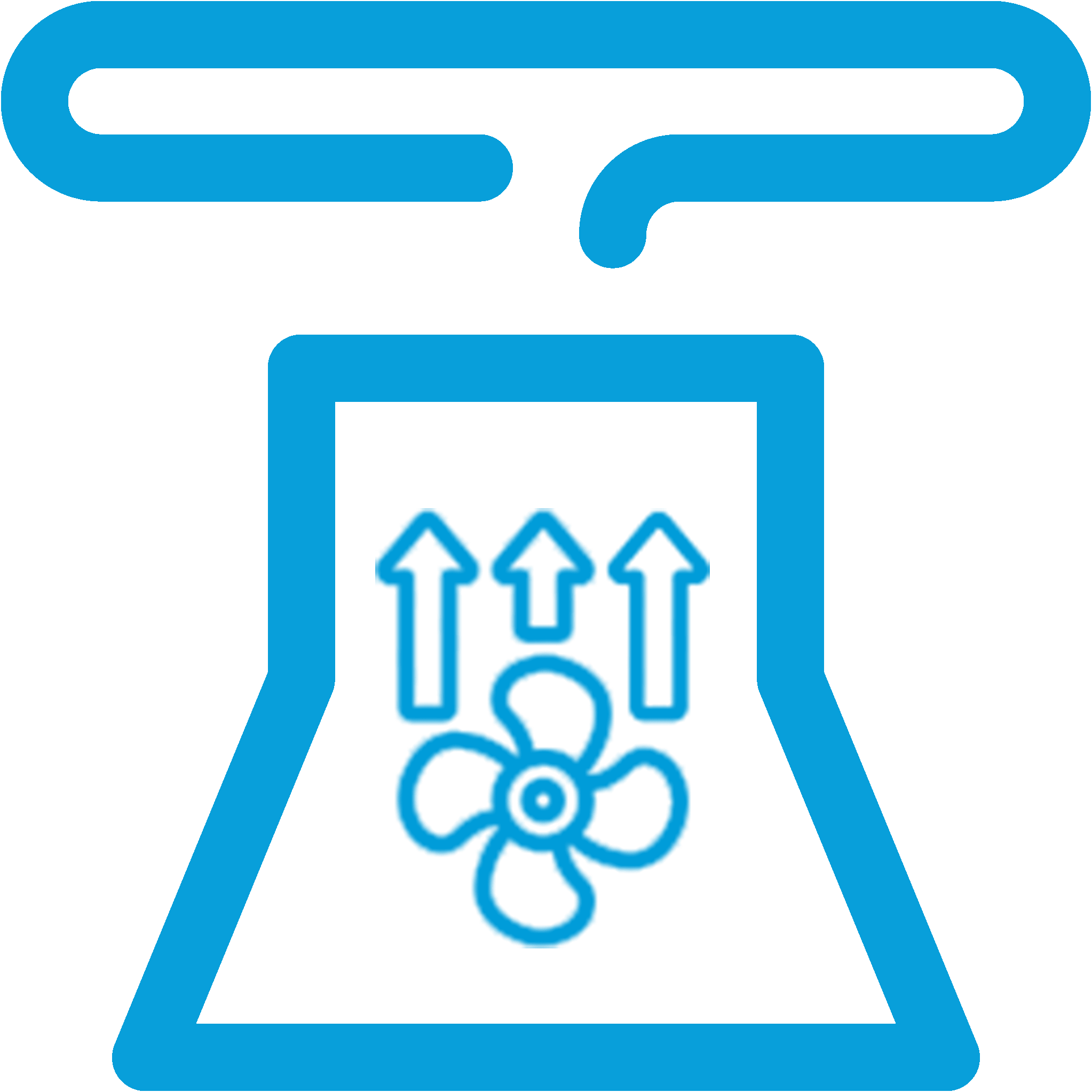
Cooling Towwer Fans
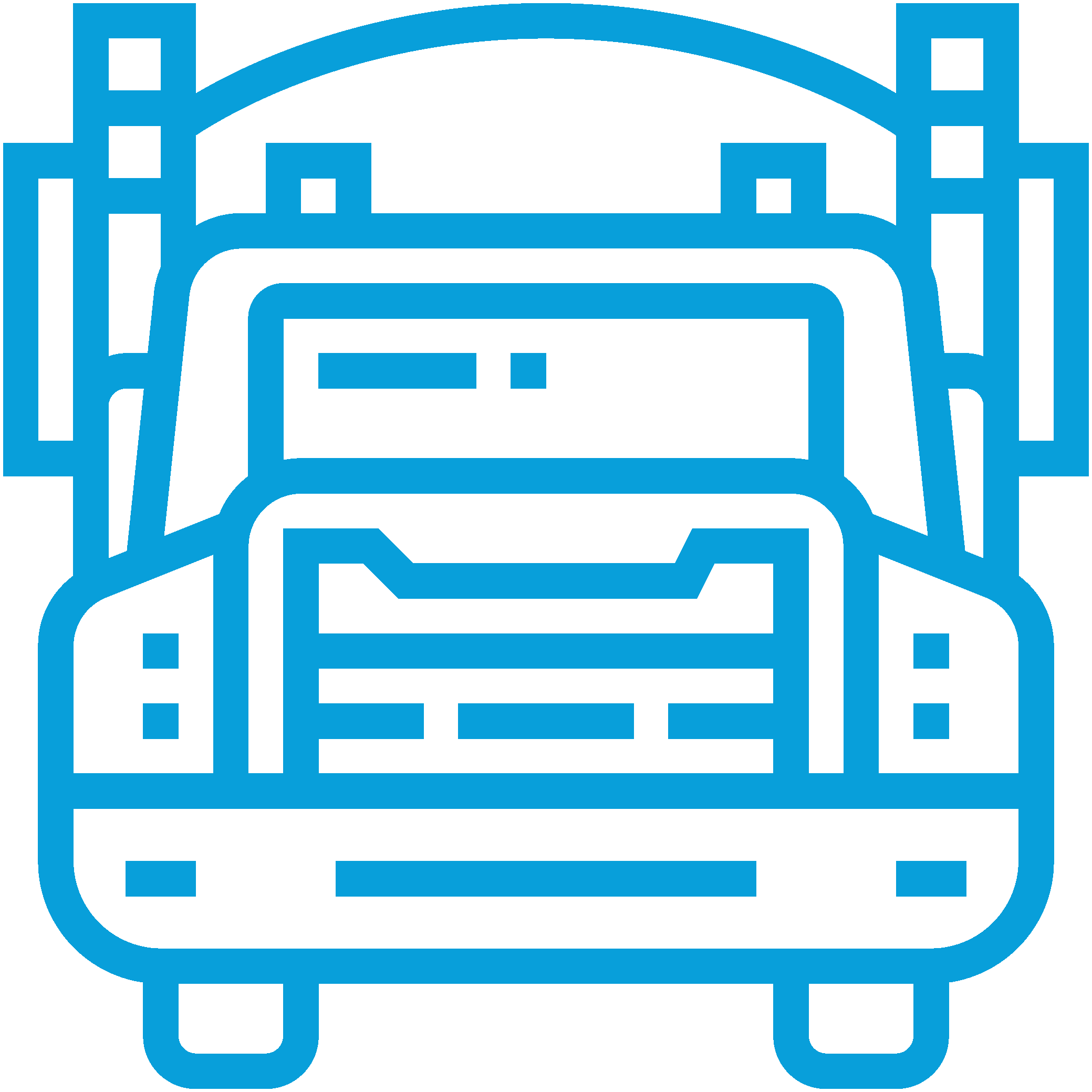
Automobile
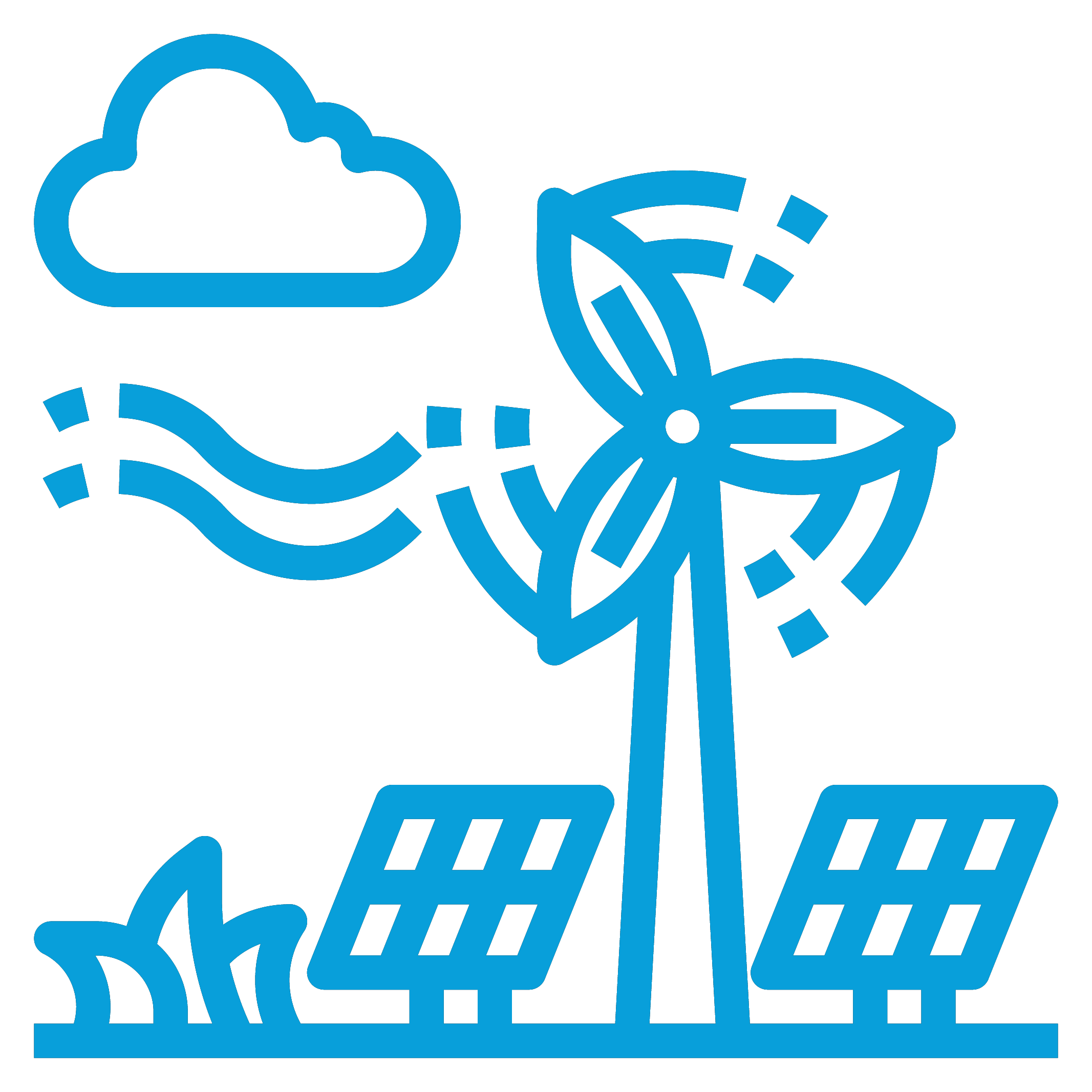
Renewable Energy
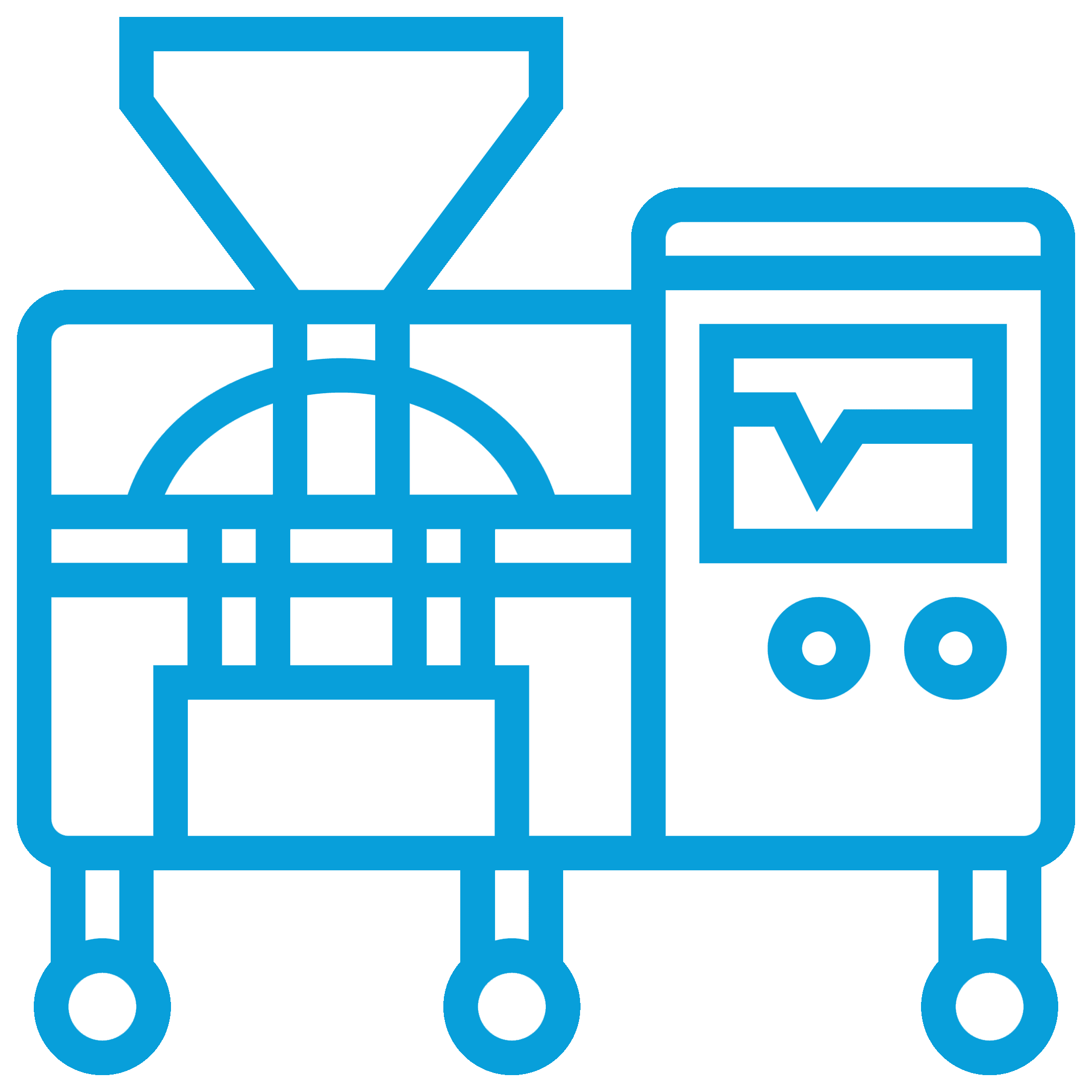
Custom Built Machinery
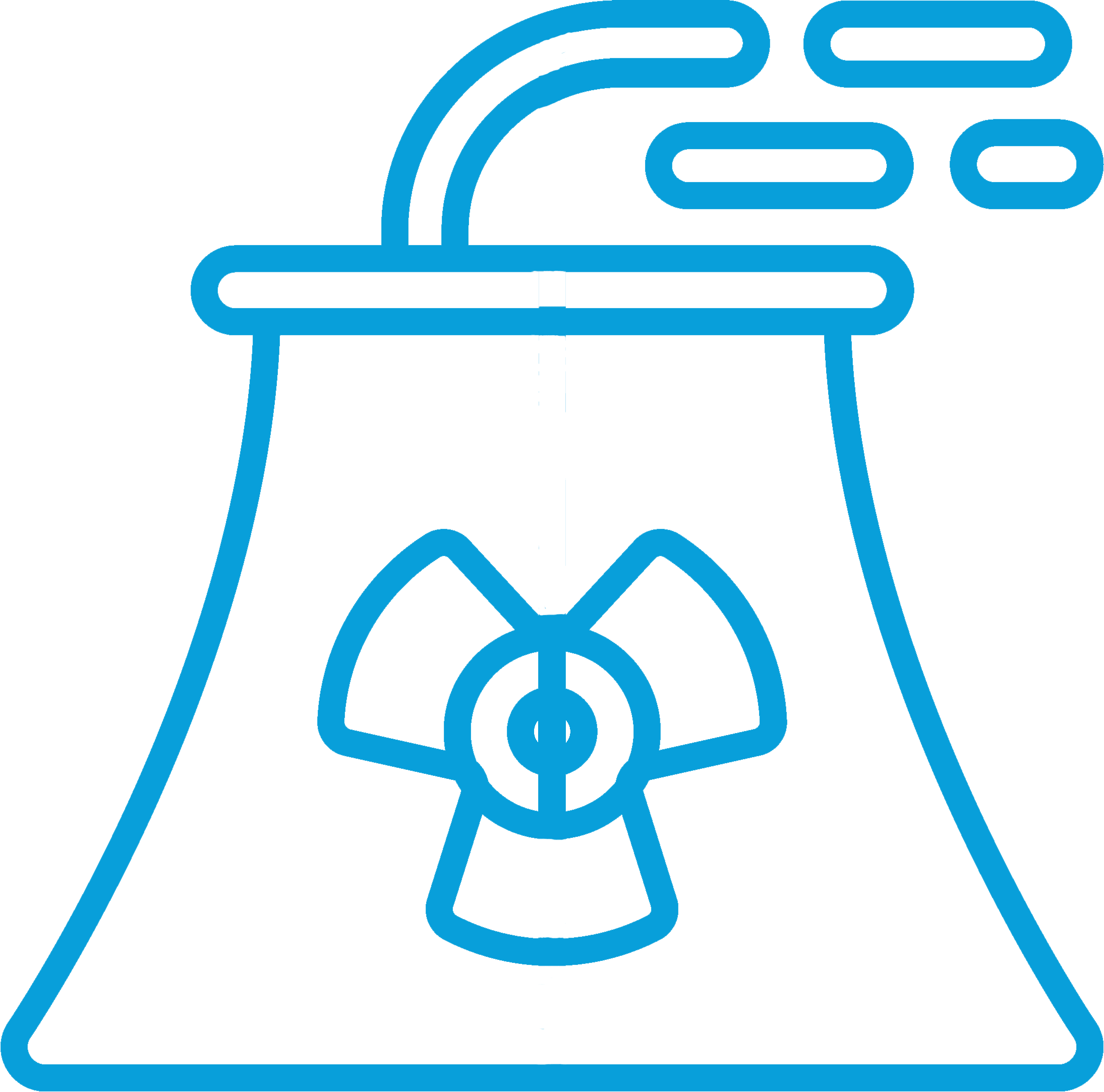
Nuclear
Value Engineering is of prime importance in the heavy equipment industry. It is the process where the value of a particular product is improved. A product’s value can be increased by improving the functions of the product. Reducing the overall cost can also be an alternative. The major steps of value engineering are (a) information phase, (b) speculation (creative) phase, (c) evaluation (analysis) phase, (d) development phase (value management proposal), and (e) presentation (report) phase. These phases are defined by the Society of American Value Engineers (SAVE).
The primary objective of the heavy equipment industry opting for design through finite element analysis is to improve performance and to achieve profitability. At Zeus Numerix, the team strives to understand the customers’ requirements. Specific emphasis is given to design constraints, performance, ease of manufacturing and possibilities of mass manufacturing. Heavy machinery is designed through finite-element based analysis. Modal, static structural, shock, random vibration, harmonic, vibration, and fatigue analyses are done. This helps to arrive at an optimal design. The machines are optimized for their structural integrity and weight. Design failure mode and reliability analysis are done to improve the overall value of the equipment.
Case Studies
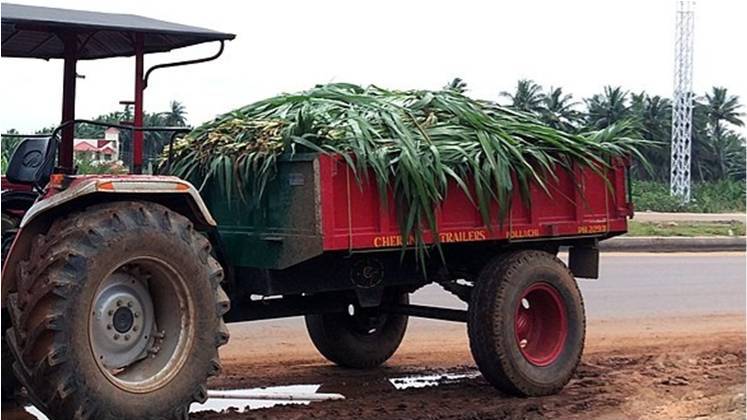
Design of Low Base Tractor Trailer
CFD studies were performed to estimate the pressure drop and pressure losses...
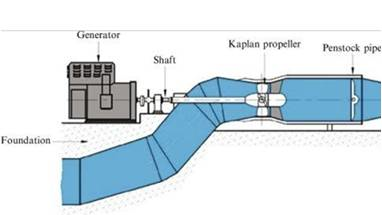
Selection & Design Consultation for 1 MW Hydel Installation
Project where micro hydro turbine plant was to be designed,developed...
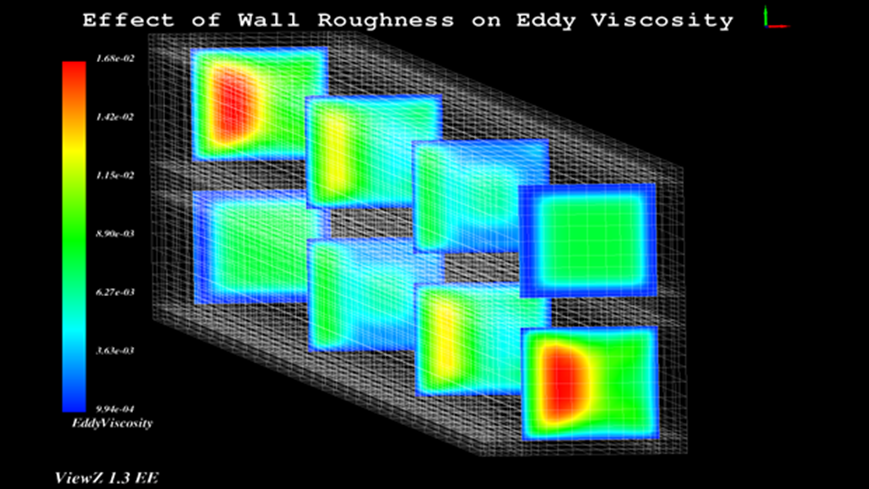
Thermal and Magneto-hydrodynamic Analysis of Thermo Nuclear Reactor Modules
CFD study to analyze the First Wall, Liquid Breeder (LLCB) and Solid Breeder...