Controls and Electronics
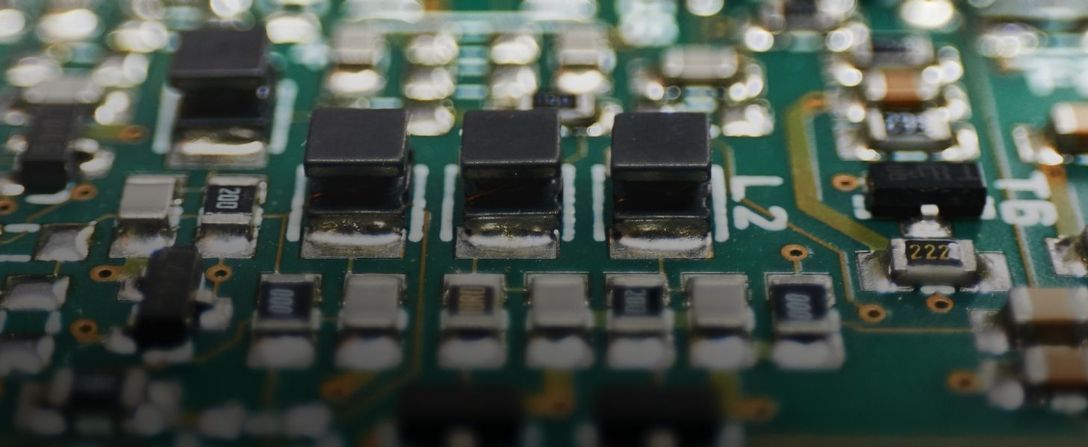
Controls and Electronics
We specialize in the field of sensing, controls and actuation for applications that demand high precision. As per requirement, our team builds custom embedded systems, by design and manufacture of PCBs specifically for extreme environments. We also develop instrumented test rigs for functional and performance trials of fluid machines and hydraulic systems. We integrate them with PLCs, SCADA, and IoT framework for real-time remote monitoring & automated control systems.
What we do
- Hardened or rugged electronics
- Programmable Logic Circuit (PLC), SCADA, test rig development
- Sensor integration, actuators, controllers
- Software programming for controllers
- PCBs, Circuits, onboard computers
Our experience
- Microcontroller for aerospace equipment
- SCADA system for air cycle machine test rig
- Controller for guided rocket and artillery shell
- UAV electronics and autopilot

Remote Monitoring
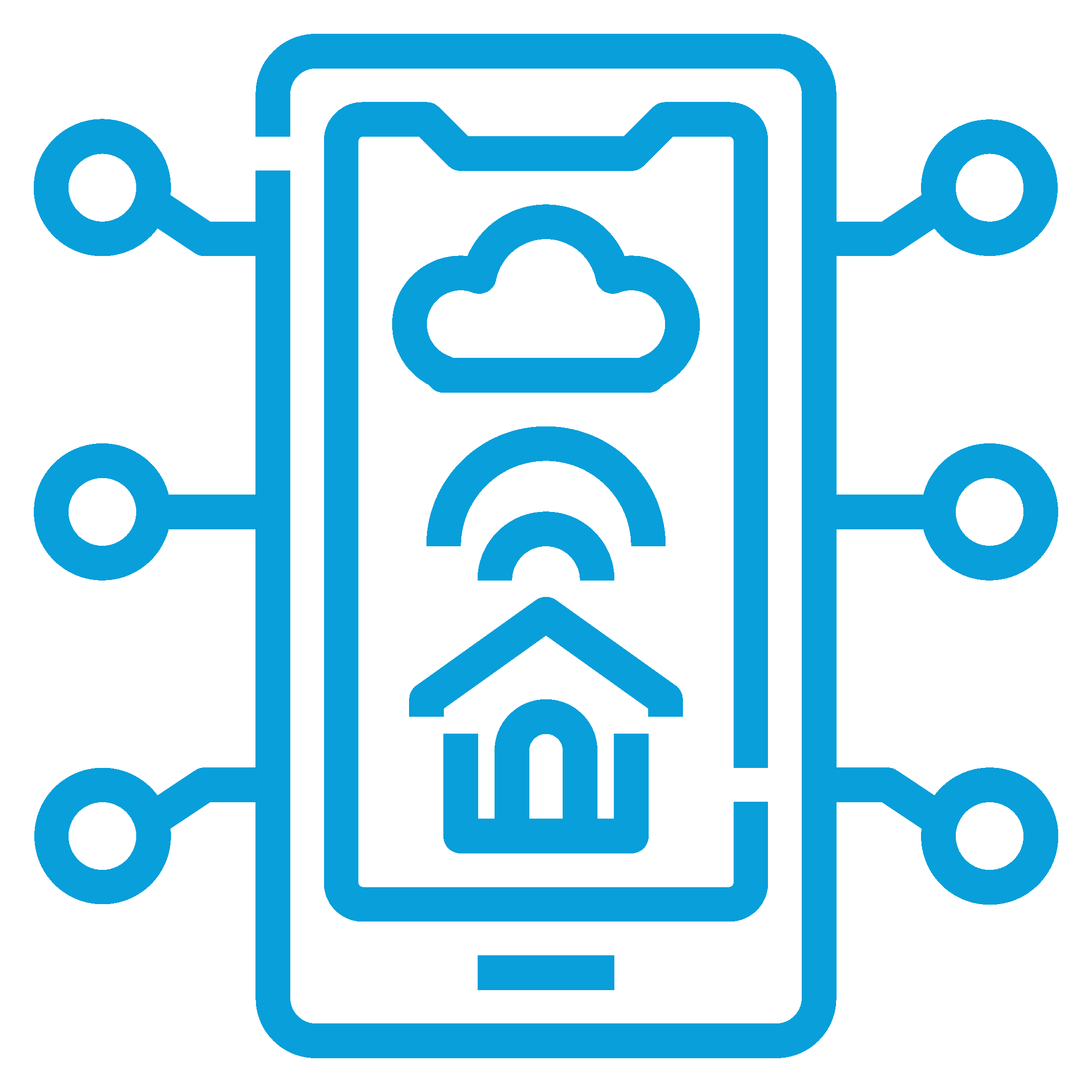
Automated Controls
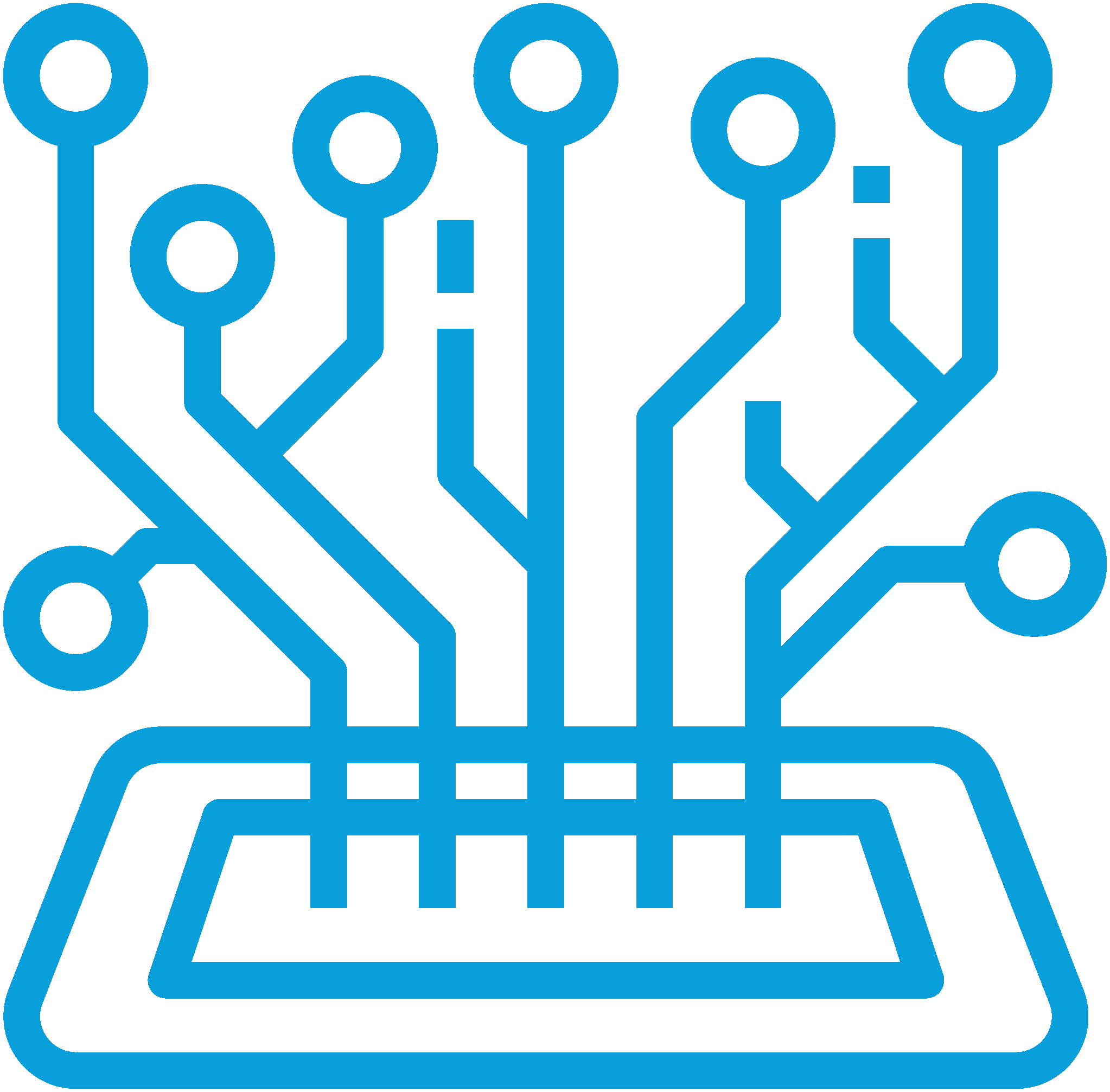
Embedded Systems
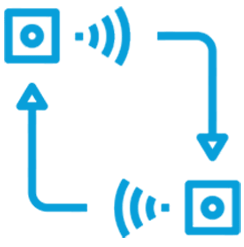
Sensors
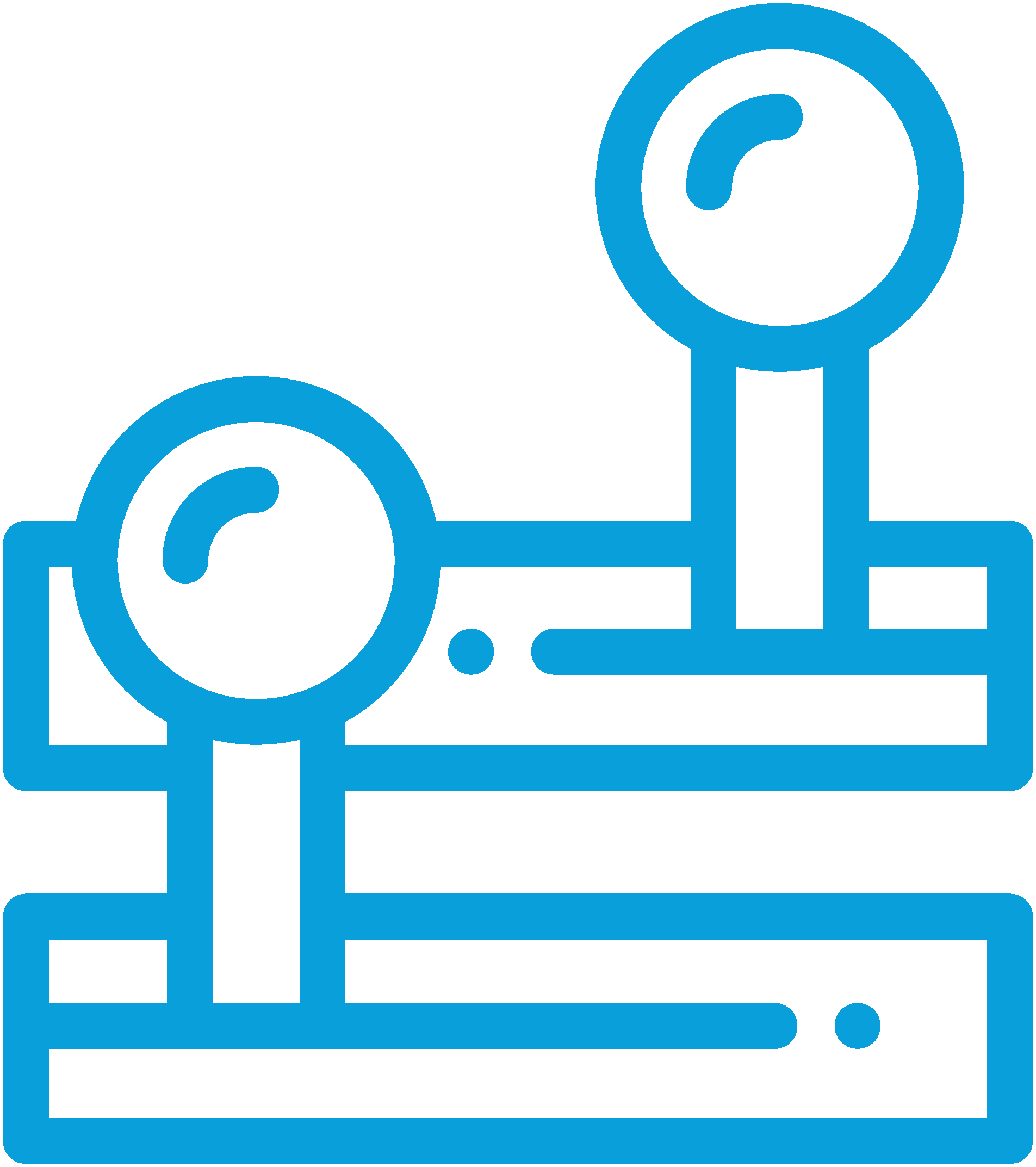
Actuators
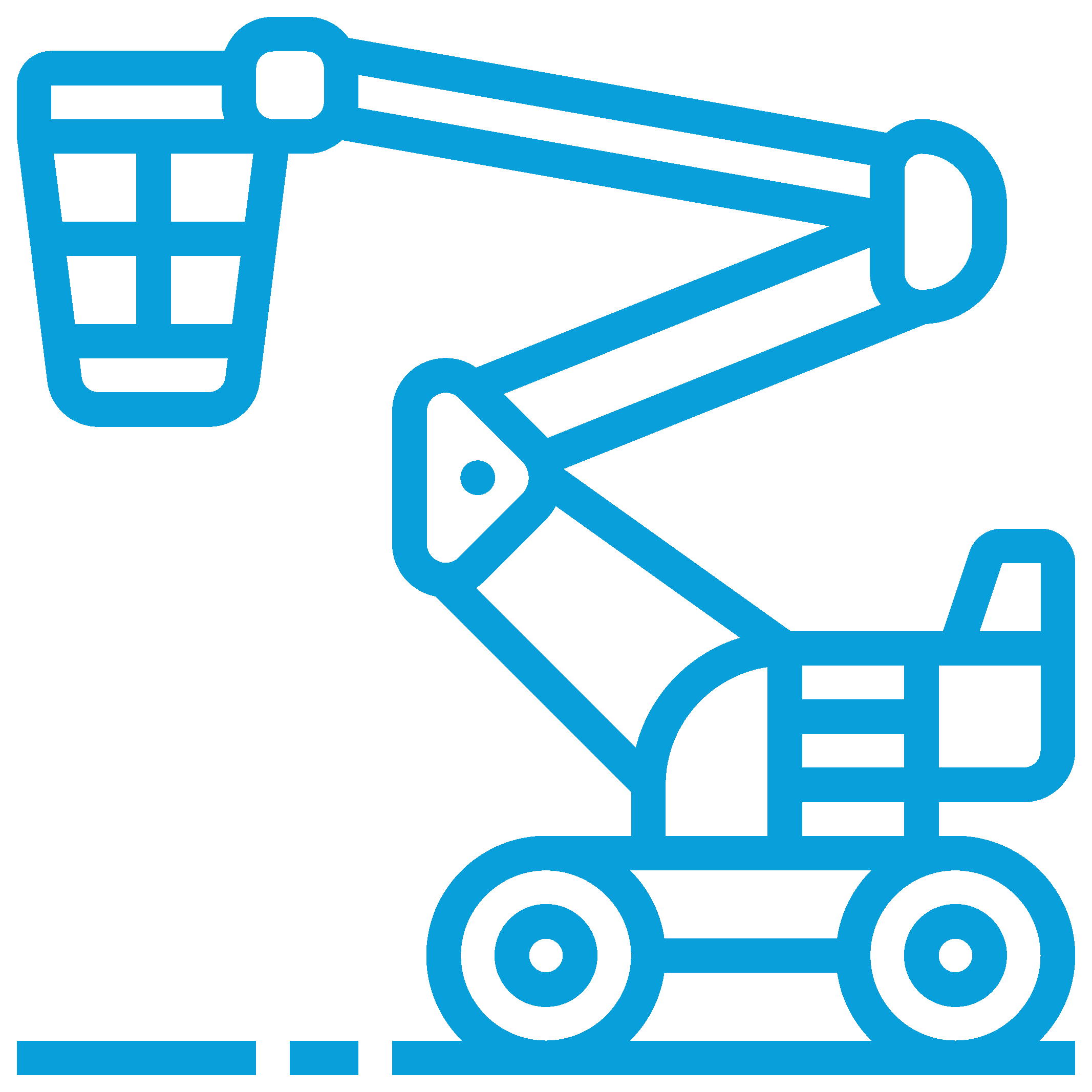
Hydraulic Systems
Design and Development of embedded systems involve five major steps/processes. They are defining requirements, specifications formulation, architecture design, building the components, and system integration. The most common components that make up an embedded system is the power supply unit, microprocessor, timers, memory, and other supporting hardware. Embedded systems engineering requires fluency in programming languages. Programming languages such as C, C++, C# are used in embedded systems engineering. Industrial processes are supervised and controlled by employing hardware-software components called SCADA. SCADA stands for Supervisory Control and Data Acquisition. Typical components in a SCADA system include five components. They are supervisory computers, remote terminal units, programmable logic controllers, communication infrastructure, and a human-machine interface.
Test rigs designed for fluid machine applications involve many types of sensors. The test rigs contain flow controllers as well. Sensors used in such test rigs include pressure sensors, temperature, load sensors. Controllers include flow control valves, pressure control valves. Regulation of temperature, pressure and flow controllers is done using PID controllers. The data measured by these sensors and controllers are routed via probes to an interface box. The interface box contains the DAQ hardware. Specialized DAQ software, reads the data measured by the DAQ hardware. It then transfers them to the cloud. The most prominent GUI development application for test rig monitoring & control is LabView.
Case Studies
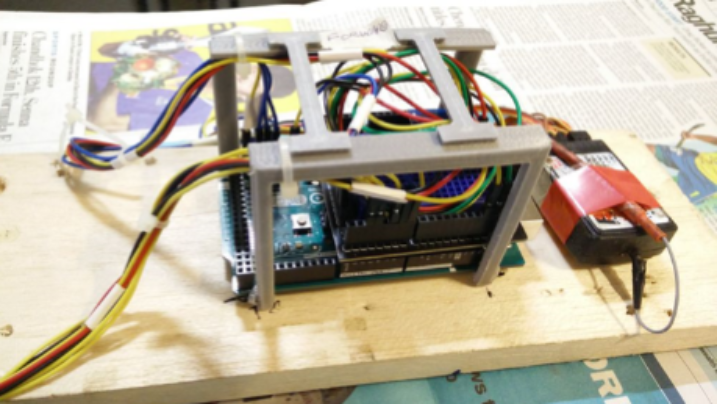
Development of Altitude Hold Controller for Airship
Development of a control algorithm and its testing on an available scaled down version...
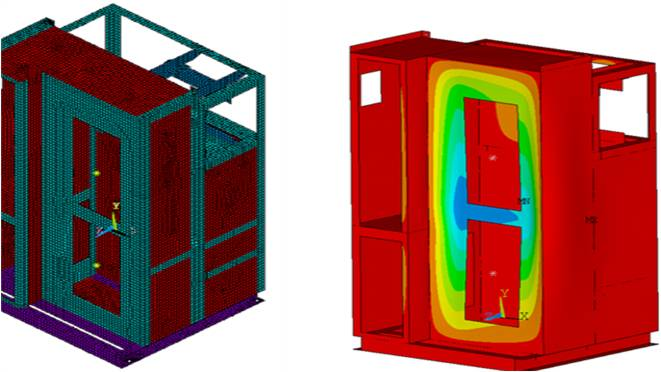
Shock and Vibration Analysis for Certification of Electronic Equipment
Certification studies for covering (a) functional analysis for random vibration in 3 directions (b) Long life...
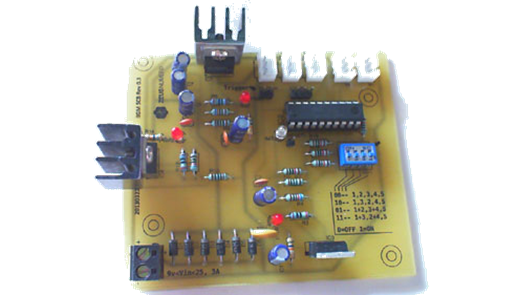
Design and Development of Micro-Controller for Probe Deployment in Space
For in-flight deployment, a servo motor-based system was required to ensure smooth and controlled...